江西跑合机价格
CNC加工中心主轴的工作原理基于电机的驱动和轴承的支撑。电机产生的动力被传递给主轴,主轴通过轴承的支撑保持稳定运转。精确的控制系统能够调节主轴的转速、进给速度和位置,实现不同类型工件的精密加工。CNC加工中心主轴的关键技术1.高速驱动技术:CNC加工中心主轴需要具备高转速的特点,以实现高效的加工。高速驱动技术包括电机的选型、传动系统的设计和优化,以及冷却系统的保障,确保主轴在高速运转时保持稳定和可靠。刚性和精度控制技术:CNC加工中心主轴需要具备高刚性和精度,以实现复杂零件的精密2加工。刚性控制技术涉及主轴结构的设计和材料的选择,以提高主轴的刚性和抗振能力。精度控制技术包括轴承的选用、控制系统的精确度,以及振动和热变形的补偿措施,以保证加工的精度和质量用工具进行压装,确保轴承的正确定位。江西跑合机价格
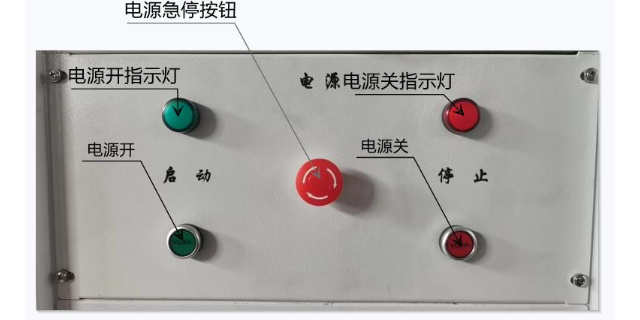
3、主要解决措施 由于主轴轴承采用的是双列短圆柱滚子轴承,该轴承内圈的内孔带有锥度,它与主轴上的锥面相结合,其调整的理想状况为内圈随着被涨大,把轴承外圈涨紧在短圆柱上,使它刚刚不因本身重力而下来,但又能灵活地转动为止。根据故障分析,问题主要出现在主轴轴承隔套的调整方面。 改进后的装配工艺方法如下: (1) 清洗主轴轴承,并将清洗槽按粗洗和精洗分开。 (2) 测量各配合件尺寸并做记录。主要测量主轴套筒前、后两孔内径尺寸,两双列圆柱滚子轴承的外圈尺寸。西藏本地跑合机定期检查和清洁主轴。
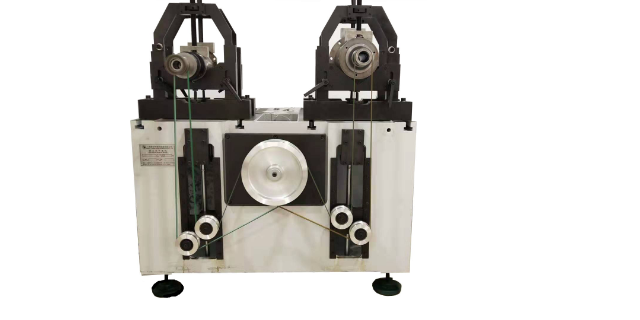
(1)拆下雕刻机主轴前后端盖及前后螺母; (2)从轴的前端向后用力推出主轴及后轴承座,直线轴承等附件; (3)轴承垫圈。 雕铣机主轴操作的基本注意事项有哪些吗? 1.雕刻过程中,严禁近距离观察,以防止切屑飞入眼睛,观察时要暂停雕刻,关闭电机主轴并确定电机主轴不再旋转。 2.雕铣机主轴维修装卡刀具时露出卡头的长度须参照雕刻工件、夹具而定,在满足条件情况下露出卡头的长度尽量的短,当刀具的总长度小于22mm时,严禁继续使用。 3.装卡刀具时,须先将卡头里的灰尘及杂物清理干净,把卡头装入压帽内并放正,再一起装到电机主轴上并将刀具插入卡头,再锁紧压帽,上下刀松紧压帽的时候严禁采用推拉方式而要用旋转方式。
2.主轴是一种复杂、精密的组合部件,也是自动化生产设备的部件,其品质的优劣直接影响到自动化设备的性能。主轴在出厂前,大都需要经过一系列的验证测试,其中,跑合测试是对主轴整体性能的检测,是众多测试中重要的一项检测。3.现有的跑合测试机,大都是将主轴安放在测试台上,模拟实际运行环境驱动主轴内芯轴旋转。但不同结构尺寸的主轴,其对驱动装置的输出要求往往不同,且模拟环境下的驱动装置的设置大都与实际情况不同,其产生的振动很可能对主轴内部结构件造成不良影响。遵循操作手册进行日常检查。
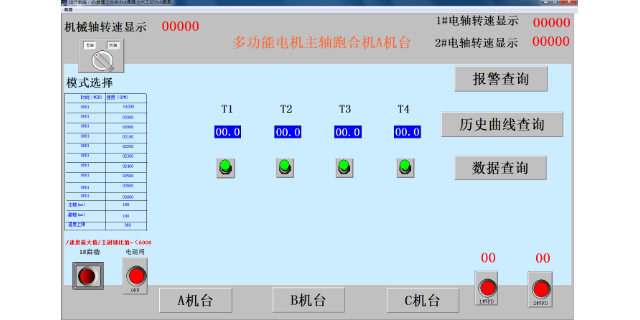
(2)故障处理:更换前轴承及润滑脂,调整轴承游隙,手工研磨主轴内锥孔定位面,用涂色法检查,更换碟形弹簧。将修好的主轴装回主轴箱,用千分表检查径向跳动,主轴温升和噪声正常,加工精度满足加工工艺要求,故障排除。 (3)改进措施:①增加压缩空气精滤和干燥装置,过滤器要定期排水,定期清洗或更换滤芯;②随时检查主轴锥孔、刀柄的清洁和配合状况,检查空气干燥器工作是否正常;③合理安排加工工艺,避免材料切除率陡变;④严禁超负荷运行,有故障应及时报修,不得带病运行。 在产品的试验过程中,发现主轴运转噪声很大,严重影响机床精度,轴承的使用寿命也缩短,通过对该产品的主轴结构和装配过程进行分析,找出装配精度超差的原因,并根据发现的问题,提出新的装配工艺方法,解决了装配精度超差的问题。 主轴采用两点支撑,主轴前端采用双列圆柱滚子轴承和双列圆柱滚子轴承组合支撑,通过锁定螺母调整轴承间隙,后端采用双列圆柱滚子轴承支撑,通过两个锁定螺母调整游隙。主轴端部短锥用于工装夹具的定位,并通过端面键传递扭矩,主轴传动通过多楔带轮经花键法兰盘传递到主轴,以消除带轮对主轴的径向张紧力,提高主轴刚度。确保设备完全断电。 使用合适的工具,拆下主轴。 标记和记录每个部件的位置,以确保重新组装的准确性。内蒙古耐用跑合机
在主轴尾端安装有一用于装卡的压力缸,该压力缸通过安装在空心主轴中的拉杆控制安装在主轴前端的装卡装置。江西跑合机价格
主轴跑合系统主要用于加工中心主轴的生产和维修过程中跑合并监测主轴的转速和温度变化。该系统可同时运行监测两套主轴的跑合老化试验,并且可分别设置连续运行监测和分段运行监测,全部自动智能化运行,无需人工调整和看守。通过主轴固定装置将新加工的主轴支撑于主轴支架上,电机带动所述主轴进行跑合,在跑合过程中,避免所述主轴加工过程中的局部加工误差和缺陷,然后调整主轴,提高主轴的回转精度;从而使得在跑合后,主轴具有较高的回转精度江西跑合机价格