超声冲击振动时效去应力
振动时效效果主要是指零件振动后残余应力消除、均化、抗变形能力的提高以及尺寸精度的稳定化程度。在生产现场常采用,根据的振幅时间(A-t)曲线采用下列方法来快速判断振动时效效果:(1)检测幅频曲线共振峰形状的变化,在幅频曲线上表现出共振峰由宽变窄: (2)检侧共振频率发生的变化; (3)检测振动过程中零件幅值及激振功率的变化,若保持激振能较不变,则振幅上升;若控制振幅值恒定.则激振功率降低。若出现上述一种情况,在实践中就判定振动时效达到了预期的目的。为了定量了解振动时效工艺效果,使用磁应力仪,检测了挖掘机平台等工件焊缝处振动时效前后的残余应力。振动时效对于机械设备、航空航天器件和汽车零部件等具有重要的影响。超声冲击振动时效去应力
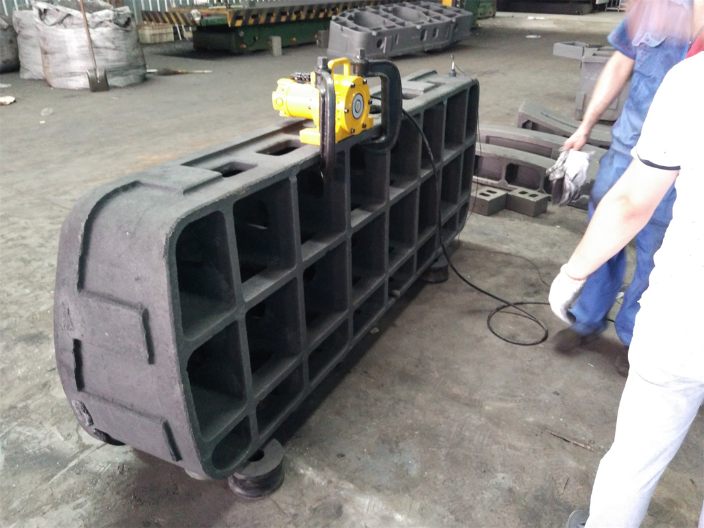
振动时效设备可以改善材料的耐腐蚀性能。振动时效过程中,材料表面会受到振动的刺激,从而促进了表面氧化膜的形成和再生。这种氧化膜可以提供额外的保护层,防止材料与外界环境中的氧、水和其他腐蚀介质接触,减少了材料的腐蚀速率和腐蚀深度。振动时效设备对材料的振动时效过程具有多方面的影响,包括提很大强度和硬度、改善韧性和断裂韧度以及提高耐腐蚀性能等。这些影响使得材料在使用过程中更加可靠和耐用。因此,振动时效设备是一种有效的材料处理方法,可以提高材料的性能和品质。浙江超声冲击震动时效设备哪家好振动时效设备可以精确地模拟产品在实际使用环境下的振动条件。
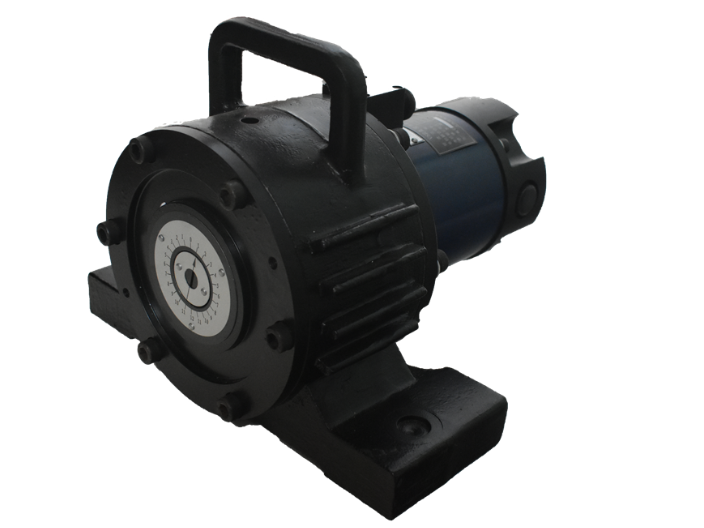
由于机床床身在铸造及粗加工后,存在有残余应力,且残余应力不稳定性,造成应力松弛和应力的再分布,使工件产生变形影响机床精度,因此需要在粗加工后进行振动时效处理消除残余应力。机床铸件应用振动时效工艺,从近百件的床身中随机抽出两件进行残余应力振前、振后测量计算,结果发现振动时效使纵向平均应力水平降低32%,横向应力降低39%,不低于热时效的效果。其抗变形能力比热时效有所提高,精度变化值与热时效相比均小于0.005mm,符合工艺要求。振动时效工艺其原理是用振动消除残余应力,可达到热时效工艺的同样效果,并在许多性能指标上超过热时效。
振动时效处理过的构件,需通过一定的评价 方法以表征其时效效果,具体指对残余应力的降 低、调控,构件抗变形能力的提高以及尺寸精度的 提高等[38]。现阶段,振动时效技术的理论基础仍有 待进一步研究,其效果难以精确测定,且没有统一 的标准。目前,已有参数曲线观测法、精度稳定性 检测法和残余应力测量法用于时效效果的评定。当构件中存在的残余应力幅值或分布发生改 变时,其自身振动状态将随之变化,因此通过测量振动时效过程中的实时振幅-时间曲线的变化及振幅-频率曲线振动前后的变化可以定性评估振动时效的效果。振动参数曲线可能发生的变化为:(a) 振幅时间(a-t)曲线上升后变平或曲线上升后下降之后变平;(b) 振幅频率(a-f)曲线振后的峰值升高;(c) 振幅频率(a-f)曲线振后的峰值点偏移;(d) 振幅频 率(a-f)曲线振后的谐振带宽变窄[39-40]。振动时效工艺能够部分地取代热时效。
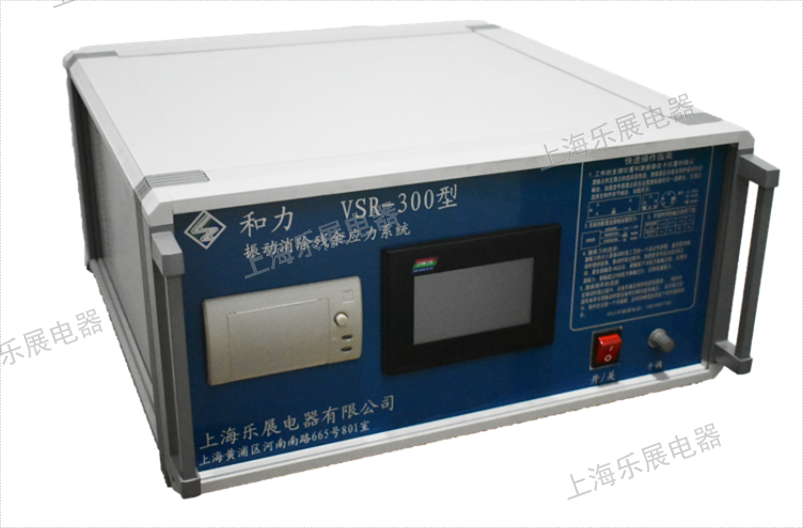
振动时效:优点:①机械性能明显提高,经过振动时效处理的构件其残余应力可以被消除20%—80%左右,高拉应力区消除的比例比低应力区大。因此可以提高使用强度和疲劳寿命,降低应力腐蚀。可以防止和减少由于热处理、焊接等工艺过程造成的微观裂纹的发生。可以提高构件抗变形的能力,稳定构件的精度,提高机械质量。②适用性强,由于设备简单易于搬动,因此可以在任何场地上进行现场处理。它不受构件大小和材料的限制,从几十公斤到几十吨的构件都可以使用振动时效技术。特别是对于一些大型构件无法使用热时效时,振动时效就具有更加突出的优越性。③节省时间、能源和费用,振动时效只需30分钟即可进行下道工序。而热时效至少需要一至两天以上,且需要大量的煤油、电等能源。因此,相对与热时效来说,振动时效可节省能源90%以上,可节省费用95%以上,特别是可以节省建造大型焖火窑的巨大投资。振动时效设备可以帮助无法在实际环境中完成测试的产品进行测试。南通应力消除震动时效仪价格
振动时效设备可以对产品的机械性能、电气性能、热性能等进行评估。超声冲击振动时效去应力
传统的消除残余应力的时效方法有热时效和自然时效。热时效是将金属放置在加热炉中,经过升温、保温和降温三个过程的温度变化,使金属迅速膨胀和收缩,降低材料的屈服极限,因而残余应力高的地方,就会超出屈服极限,使晶格滑移,产生微小的塑性变形,从而将残余应力释放、降低和均化。热时效需要的加热炉,投资大、能耗大、效率低、污染环境、容易产生新的变形和二次应力。自然时效是将金属长期放置露天,利用昼夜的温差和复杂多样的“环境震荡”,使金属发生缓慢、细微的收缩和膨胀,经长期积累得到释放残余应力的目的。自然时效周期长,效率低,导致成本增加。超声冲击振动时效去应力
上一篇: 上海塑胶件应力怎么消除
下一篇: 上海结构件震动时效设备哪家专业