非标准跑合机批量定制
主轴跑合系统主要用于加工中心主轴的生产和维修过程中跑合并监测主轴的转速和温度变化。该系统可同时运行监测两套主轴的跑合老化试验,并且可分别设置连续运行监测和分段运行监测,全部自动智能化运行,无需人工调整和看守。通过主轴固定装置将新加工的主轴支撑于主轴支架上,电机带动所述主轴进行跑合,在跑合过程中,避免所述主轴加工过程中的局部加工误差和缺陷,然后调整主轴,提高主轴的回转精度;从而使得在跑合后,主轴具有较高的回转精度使用专门的平衡机检测主轴的平衡状况。非标准跑合机批量定制
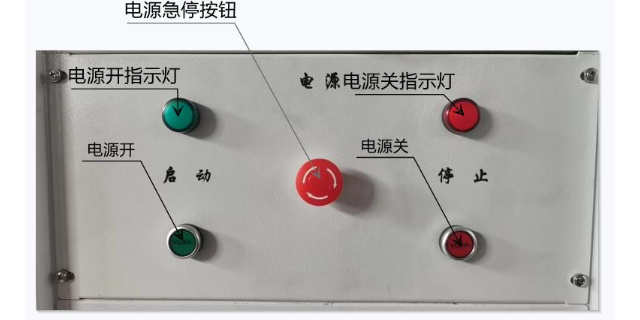
由于轴承内有高速油脂,在运输过程中或长时间不使用,油脂状态会改变,通过磨合使油脂纤维沿轴承运转方向顺序排列,可以降低发热,并使轴承得到较好的润滑,从而使主轴电机正常运转。如果不磨合直接高速启动,由于润滑条件不好,就会产生噪音、刺耳的尖叫声、发热等现象,甚至会损伤轴承,降低使用寿命。当电机、维修后的电机开始使用时,或电机使用中出现扎刀的问题时或停机两天以上的时间重新使用时,进行磨合工作!主轴磨合基本山西自动化跑合机在主轴箱上部的床身上固定有施压装置,施压装置由压力缸和压力缸活塞杆端部安装的施压头组成。
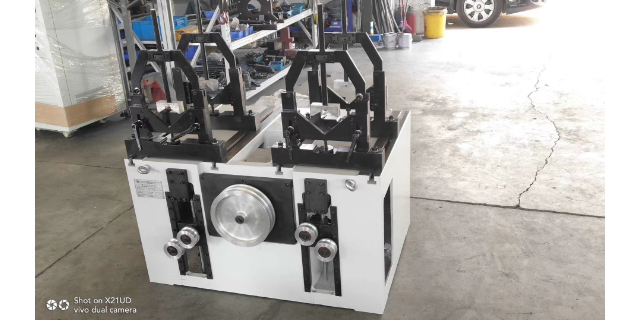
从主体上看,加工中心主要由以下几大部分组成:1.基础部件基础部件是加工中心的基础结构,它主要由床身、工作台、立柱三大部分组成。这三部分不仅要承受加工中心的静载荷,还要承受切削加工时产生的动载荷。所以要求加工中心的基础部件,必须有足够的刚度,通常这三大部件都是铸造而成。2.主轴部件主轴部件由主轴箱、主轴电动机、主轴和主轴轴承等零部件组成。主轴是加工中心切削加工的功率输出部件,它的起动、停止、变速;变向等动作均由数控系统控制;主轴的旋转精度和定位准确性,是影响加工中心加工精度的重要因素。3.数控系统加工中心的数控系统由CNC装置、可编程序控制器、伺服驱动系统以及面板操作系统组成,它是执行顺序控制动作和加工过程的控制中心。CNC装置是一种位置控制系统,其控制过程是根据输入的信息进行数据处理、插补运算,获得理想的运动轨迹信息,然后输出到执行部件,加工出所需要的工件。
可以看出,刀夹1被夹持的动力主要来自碟形弹簧18的弹力,刀夹1轴向定位的拉紧力主要来自碟形弹簧20的弹力,刀夹1的松开由主轴后端的液压缸提供动力。当液压缸右腔进入液压油时,液压缸中的活塞23向左移动,其左端面首先推动拉杆左移,同时碟形弹簧20被压缩,拉杆9左端的定位套筒7左移(此时固定在主轴11上的定位小轴6因主轴不动而不移动)。由于定位套筒7左移,使钢球4进入套筒3(套筒3也不移动)的大直径部分,使得刀夹1由拉紧状态变成放松状态,而且在拔取刀夹1时,钢球4能径向退让开。当活塞23继续左移时,使左端面外圈与拉套10的右端面接触,且活塞23再向前移动压缩碟形弹簧18并推动拉套10向左移,从而使与拉套10相连的弹赞夹头2同时向左移动而松开,刀夹1即不再受夹紧力,并可从主轴中取出。电气参数变化、接近开关松动等原因造成的。

新机器所有系统都是新的,还会有多余的润滑油脂,如果刚开始电机主轴就进行高负荷运行,那么机器它的零件磨损和间隙就会加大,所以需要磨合,使它的润滑系统适应工作强度。在常年恒温的房间里主轴电机由慢速逐步增加到主轴的高转速,需要进行一段长时间的跑合程序用来观察主轴性能的稳定情况,确保滚动体与轨道之间的有效磨润,在这个跑合的过程当中,有转速的控制,还有震动的控制,这些都会得到相应的测试数据,通过量化加载和在线监测,图表分析等等,更科学的反应机床主轴的传动系统的制造和装配质量,方便我们的技术人员对产品进行技术改造和产品更新跑合为使机械零件表面轮廓峰形状变化及零件材料表面加工硬化。机床主轴跑合机大概多少钱
加工中心的主轴是关键部件之一,其运行状态直接影响加工质量和设备寿命。同时也会缩短主轴的使用寿命。非标准跑合机批量定制
1、刀具自动夹紧装置。刀具自动夹紧装置中刀夹1的内孔用来安装刀具,刀夹1的夹紧与松开动作由弹簧夹头2和轴向拉紧机构控制。弹簧夹头2与拉套10采用螺纹联接,拉套10左端螺纹部分开有轴向槽,其内孔为锥孔,锁紧件8旋入拉套10左端内螺纹孔内,在锁紧件8外锥体的作用下,拉套10开有轴向槽的螺纹部分与弹簧夹头2上的螺纹联接锁紧。主轴11后端有碟形弹簧18,在弹簧力的作用下,拉套10向右拉紧弹簧夹头2,将刀夹1紧紧夹住。为使刀夹1在主轴孔内准确定位,固定在主轴11上的定位小轴6上有一颗定位螺钉5,其端面是刀夹1的轴向定位面。装在拉杆9右端的碟形弹簧20,使拉杆9经常承受向右的弹簧力,固定在拉杆9左端的定位套筒7内的钢球4就将刀夹1右端轴颈夹持并向右拉动,直至刀夹1右端面紧靠在定位螺钉5的定位端面上。非标准跑合机批量定制
上一篇: 立式平衡机哪家强
下一篇: 内蒙古平衡机欢迎选购