奉贤区锌合金压铸工艺
压铸锌合金的主要添加元素有铝,铜和镁等。锌合金按加工工艺可分为形变与铸造锌合金两类.铸造锌合金流动性和耐腐蚀性较好,适用于压铸仪表,汽车零件外壳等。压铸锌合金以锌为基加入其他元素组成的合金。常加的合金元素有铝、铜、镁、镉、铅、钛等。锌合金熔点低,流动性好,易熔焊,钎焊和塑性加工,在大气中耐腐蚀,残废料便于回收和重熔;但蠕变强度低,易发生自然时效引起尺寸变化。熔融法制备,压铸或压力加工成材。按制造工艺可分为铸造锌合金和变形锌合金。锌合金压铸工艺对操作工人的技能和素质要求较高。奉贤区锌合金压铸工艺
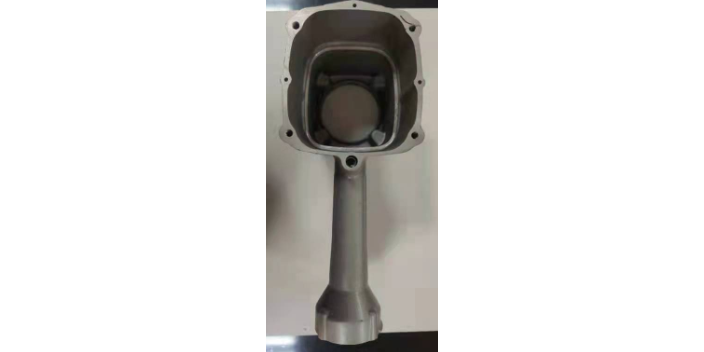
1试验材料及设备试验以纯金属Zn99.99%、Al99.85%、Cu99.90%、Mg99.80%为原材料,干燥的木炭为覆盖剂,工业用氯化铵为精炼剂。采用马弗炉—石墨粘土坩埚熔制合金并铸锭,工业试验选择在750kg工频无芯感应电炉内进行。2试验工艺已有的压铸锌合金熔炼工艺有两种:一种是先熔铜再加铝锌镁的一步熔炼法;另一种是预先熔制Al-Cu中间合金再熔制锌合金的两步熔炼法。前者由于须在超过1000℃的高温下操作,故生产中很少采用;后者虽被***采用,但仍有高温操作且工序较为繁杂的缺点。为此,我们分析提出了合金的低温直接熔炼新工艺,即先将所需铜量加入锌熔体熔化,再依次加入铝镁和剩余锌量。该法能克服老工艺的不足,试验制取的合金锭经检测质量完全合格。江苏加工锌合金压铸上海哪家锌合金压铸值得信赖?
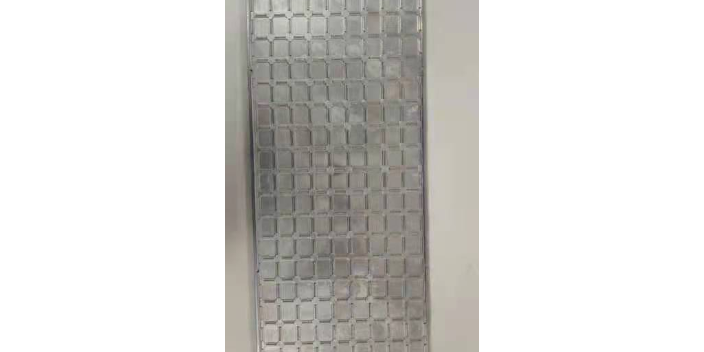
一般说来,锌合金压铸件所包含的元素有:铜、硅、镁、锌、锰等重要金属元素,还有镍、铁、钛、铬、锂等次要金属元素。而铝合金压铸件所包含的元素则有:铝、铜、镁、镉、铅、钛等常见的金属元素。由于铝合金压铸件的密度相对较低,但与之相反的强度却相对较高。其强度甚至比起一些质量的钢材还要优越,而且其可塑性优良,容易被制作成各种用途的铝合金压铸件。另外,其导电性、导热性和抗腐蚀性都相当优良,所以不但在模具压铸业上、甚至在工业上都被广泛应用,到目前为止排在钢之后的就是铝合金压铸件了。由于锌合金压铸件包含种种金属元素的原因,造就了锌合金压铸件的熔点低、拥有良好的流动性、因而熔焊方便的特性,这对制作锌合金压铸件压铸起到了相当大的作用。
由于锌合金良好的压铸性能和机械性能,因此在热室压铸中-直保持重要地位。锌合金的优点是熔点低、熔化和保温较方慢,压室和压铸型壁受热少。如何才能减少缺陷,制造出符合要求的锌合金压铸件,主要有五个方面的因素的影响。压铸机是压铸生产的关键设备,其性能的好坏客观决定了压铸件的优劣。正确选择压铸机,对保证产品质量、提高生产效率、降低生产成本至关重要,压铸机的性能取决于两个方面。足够的锁模力:防止金属溶流压力比较高峰,出现飞边、飞料。足够的注射能力:保证压铸时不造成I模过热或大量溢流,同时保证机器具有充分能力输送足够的熔融金属,并在短时间内以所需的速度,填充型腔锌合金压铸的生产过程需要严格控制温度、压力和时间等参数。
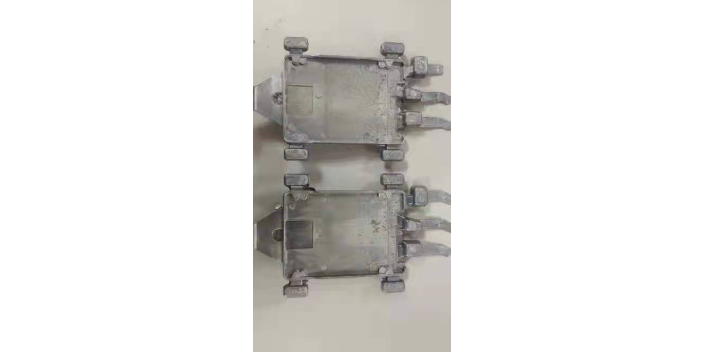
控制锌合金压铸件的表面温度对于生产高质量的压铸件至关重要。锌压铸模具温度不均匀或不适当也会导致铸件尺寸不稳定。在生产过程中,铸件发生变形,产生热压、粘模、表面凹陷、收缩、热气泡等缺陷。锌合金压铸模具控温直接影响着锌合金压铸件质量的好坏,锌合金压铸模温机能有效提高锌合金压铸件的质量。(1)压铸模具的温度过高容易导致锌合金压铸件出现粘模,出现变形;(2)压铸模具的温度过高会导致脱模剂的分解加速,造成成本的增加以及脱模效果差;(3)压铸模具的度控制不当会导致锌台金压铸件内部出现缩孔;(4)压铸模具的度控制不当容易导致锌合压铸件表面生成气泡;(5)压铸模具的温度过高容易导致模具损坏。今当锌压铸模温差较大时,会影响生产周期中的充型时间、冷却时间和喷涂时间等变量。会有冷线,主要是因为前面的熔化汤的温度太低,当有痕迹时,它们重叠。有一些细节。上海锌合金压铸的价格是多少?浦东新区高精密锌合金压铸工艺
锌合金压铸常见的用途有哪些?上海松恒告诉您。奉贤区锌合金压铸工艺
锌合金是以锌为基础加入其他元素组成的合金,常加的合金元素有铝、铜、镁、镉、铅、钛等。锌合金熔点低、流动性好、易熔焊、钎焊和塑性加工,在大气中耐腐蚀,残废料便于回收和重熔,但蠕变强度低,易发生自然时效引起尺寸变化。熔融法制备,压铸或压力加工成材。锌合金按制造工艺可分为铸造锌合金和变形锌合金。铸造锌合金流动性和耐腐蚀性较好,适用于压铸仪表,汽车零件外壳等。1.相对比重大。2.铸造性能好,可以压铸形状复杂、薄壁的精密件,铸件表面光滑。3.可进行表面处理:电镀、喷涂、喷漆、抛光、研磨等。4.熔化与压铸时不吸铁,不腐蚀压型,不粘模。5.有很好的常温机械性能和耐磨性。6.熔点低,在385℃熔化,容易压铸成型。奉贤区锌合金压铸工艺
上一篇: 上海加工锌合金压铸模具设计
下一篇: 江西摩托车锌合金压铸按需定制