真空腔体加工服务方案
腔体加工的质量控制与检测是确保产品性能的关键环节。加工过程中,需严格控制切削力、切削温度、刀具磨损等因素,避免产生变形、裂纹等缺陷。加工完成后,还需通过三坐标测量机、激光扫描仪等高精度检测设备,对腔体的尺寸、形状、位置精度等进行全方面检测,确保产品符合设计要求。此外,无损检测技术如X射线检测、超声波检测等,也常用于检测腔体内部难以直接观察的结构缺陷,为产品质量提供有力保障。随着环保意识的增强,绿色制造理念逐渐渗透到腔体加工领域。这包括选用环保型切削液、优化切削参数以减少能耗和废弃物排放、采用可回收或生物降解的材料等。同时,通过提高加工效率和精度,减少废品率和返工率,也是实现绿色制造的重要途径。此外,开发和应用新型加工技术,如干式切削、低温切削等,进一步降低了加工过程中的环境影响,推动了腔体加工行业的可持续发展。腔体加工技术的不断创新,为传统产业的升级提供了可能。真空腔体加工服务方案
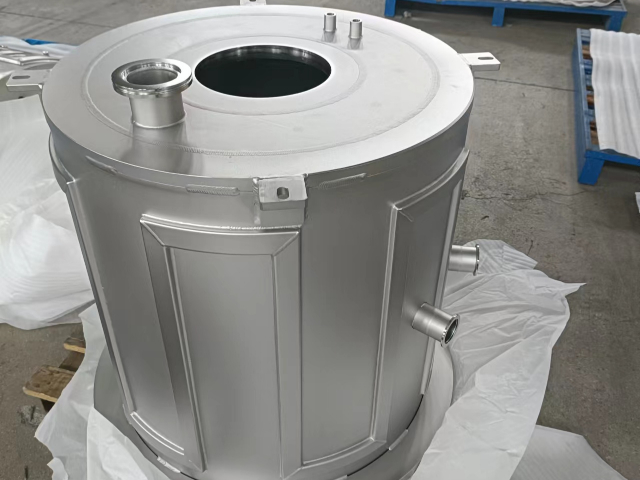
多边形真空腔体的加工首先始于精细的设计与规划阶段。由于多边形腔体在结构和功能上的独特性,设计师需根据客户的具体需求,如使用场景、压力要求、温度控制等因素,进行详尽的图纸设计。此阶段还需考虑加工的可行性与成本效益,确保设计既满足技术要求又经济合理。多边形的设计还需特别注意边角处理,以减小应力集中,提高腔体的整体稳定性。材料选择是多边形真空腔体加工中的重要环节。不锈钢、铝合金等金属材料因其良好的耐腐蚀性、机械强度和加工性能,常被用作腔体材料。在确定材料后,需进行严格的预处理,包括表面清洗、去油、除锈等步骤,以确保材料表面干净无杂质,为后续加工打下良好基础。对于铝合金材料,还需特别注意其焊接性能,以保证焊接质量。江苏D型真空腔体加工腔体加工的每一个细节都充满了挑战,但也是机遇所在。
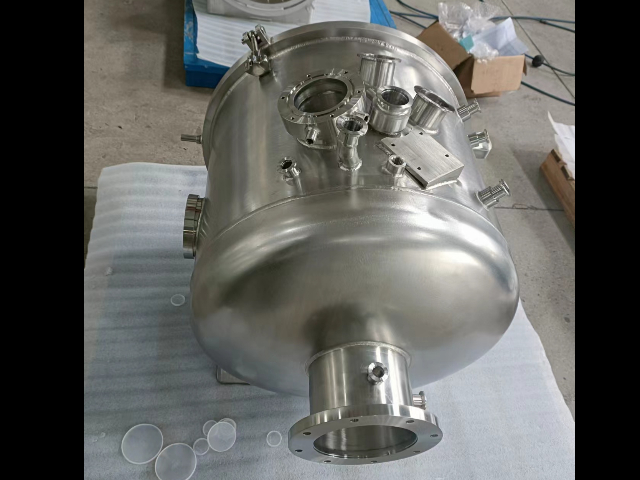
D型真空腔体的加工涉及多种精密加工技术,包括数控铣削、电火花加工、线切割等。特别是针对腔体内部的复杂曲面和精密孔道,需要采用五轴联动数控机床进行高精度加工,确保形状精度和位置精度同时达标。此外,为了满足真空密封要求,还需对密封面进行超精密研磨和抛光处理,以减少漏气率,提高腔体的真空保持能力。加工完成后,D型真空腔体-2.1需经过严格的真空性能测试。这包括使用高灵敏度真空计测量腔体的极限真空度和漏气率,以及在不同温度和压力条件下的性能稳定性测试。通过模拟实际工作场景,检验腔体是否能在极端条件下保持稳定的真空环境,确保满足设计要求和使用需求。
还需对腔体进行表面处理,如喷涂耐腐蚀涂层、镀膜等,以提高腔体的耐腐蚀性和使用寿命。精加工完成后,需对腔体进行严格的质量检验,确保其满足设计要求。多边形真空腔体的装配与测试是加工流程中的关键步骤。在装配过程中,需按照设计要求将各个部件准确无误地组装在一起,确保腔体的密封性和稳定性。装配完成后,需对腔体进行严格的测试,包括真空度测试、压力测试、温度测试等,以验证腔体的各项性能指标是否达到设计要求。测试过程中还需注意记录数据,以便后续分析和改进。严格的质量管理体系,保障腔体加工品质。
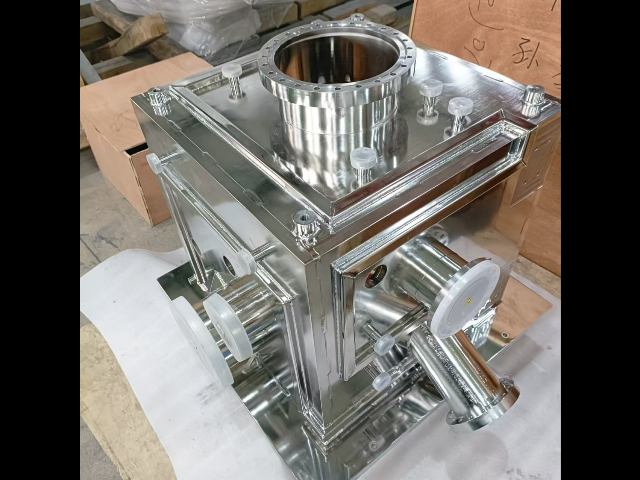
在高科技制造领域,表面清洁度对于产品质量及性能至关重要。等离子清洗机作为一种先进的表面处理技术,凭借其高效、环保、无损等优点,在半导体、航空航天、电子封装等多个行业中得到了普遍应用。其中,铝合金真空腔体作为等离子清洗机的重要部件之一,其加工精度与表面质量直接影响到设备的整体性能和稳定性。铝合金材料因其良好的导热性、耐腐蚀性以及相对较轻的重量,成为制造真空腔体的理想选择。在设计等离子清洗机的铝合金真空腔体时,需综合考虑多方面因素。首先,需确保腔体结构能够满足真空密封要求,以维持清洗过程中必要的低气压环境。其次,腔体的壁厚需经过精确计算,既要保证足够的强度以抵抗内外压差,又要避免过厚导致材料浪费和加热不均。此外,还需考虑腔体的可维护性和可扩展性,便于后续升级和故障排查。为了实现这些目标,常采用先进的CAD/CAM软件进行三维建模与仿真分析。高效冷却系统,保障腔体加工持续稳定。立式真空储气罐加工服务商
严格的加工参数控制,确保腔体尺寸精度。真空腔体加工服务方案
众所周知,在铝合金真空腔体加工完成后,还需进行一系列表面处理以增强其性能。一方面,通过阳极氧化处理在铝合金表面形成一层致密的氧化膜,提高耐磨性、耐腐蚀性和绝缘性。另一方面,针对等离子清洗机的特殊需求,可对腔体内壁进行特殊处理,如喷涂防粘涂层或进行微纳结构加工,以优化等离子体分布,提高清洗效率。此外,表面清洁度的控制也是不可忽视的一环,需采用超声波清洗、真空干燥等方法彻底去除加工过程中残留的油污、尘埃等杂质。真空腔体加工服务方案
上一篇: 浙江半导体真空腔体铝合金哪里买
下一篇: 真空铝合金腔体制造商